Automotive Ethernet vs Ethernet - What’s the Difference?
November 28, 2021
Yuri Friedman
Product Manager
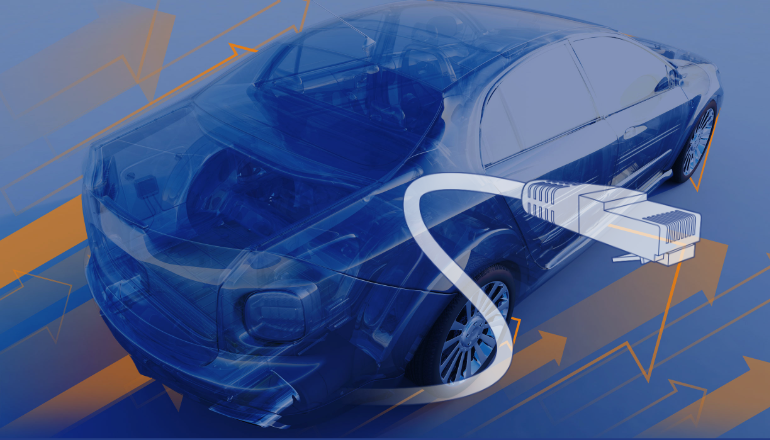
With the rise of smart cars and increased connectivity, the automotive ethernet industry is seeing a boom of its own and is expected to reach $5.6 billion by 2026.
To meet drivers’ changing demands, the communication requirements inside cars have become much more complex, more than legacy technology systems can handle. The sheer number of ECUs necessary to run everything from power steering to remote maintenance has become unmanageable for the traditional CAN set-up. Add in security concerns stemming from risks of hackers and malware, and it’s clear that new technologies are needed.
The power, simplicity and scalability of Ethernet has made it the obvious choice to bolster the outdated technology used in cars and to serve as the backbone for the new highly-connected cars.
A Brief History of Ethernet
Ethernet was originally developed in 1973 as a way to enable workstations, printers and the internet to all communicate with each other. Ethernet’s popularity has grown over time until it displaced most other options to become the technology of choice in Metropolitan Area Networks (MAN), industrial communication, broadband access and the internet backbone. Ethernet’s flexibility means it can handle speeds from 10Mbps to 400Gbps using a variety of media from coaxial cable to fiber optic transmissions.
The name Ethernet refers to the historical perception of the ether as the medium in which electromagnetic waves propagate.
The power of Ethernet moved quickly from just connecting computers and printers to becoming an integral part of the infrastructure in many industries. Based on its success in avionics, it is clear that the technology can have a similar effect in the automotive industry, especially as automotive needs become more complex and extend beyond the capabilities of the standard CAN bus.
Automotive Ethernet vs. Ethernet
Ethernet is becoming a reality in automotive as it can handle large amounts of data without adding additional complex wiring and weight to the vehicle. But traditional Ethernet is sensitive to interference, making it less than ideal for the harsh conditions found in cars: temperature, mechanical stress and electromagnetic compatibility (EMC) all present unique challenges and conditions that had to be taken into consideration, and thus a family of new Ethernet versions was standardized.
The fundamental difference between automotive Ethernet vs. Ethernet in its traditional form involves the cables: standard Ethernet uses two twisted pairs, one for transmitting data and one for receiving. Automotive Ethernet, on the other hand, uses only one twisted pair that transmits and receives at the same time. The automotive ethernet cables are also much shorter in length to account for the unforgiving environmental conditions in the vehicle. Automotive Ethernet also uses a different type of signal encoding to transmit the maximum amount of data using the least amount of bandwidth.
Implementation of Automotive Ethernet
Despite the introduction of a new standard of Ethernet specifically for the automotive industry and its clear advantages, the industry is already heavily invested in legacy networks such as CAN and is unlikely to make a complete change quickly. This means that there is going to be an intermediate period in which automobiles will be equipped with a mix of Ethernet and non-Ethernet ECUs. During this transition, both technologies will be used in tandem and it remains necessary for both protocols to be supported.
Benefits of Automotive Ethernet
While the automotive industry will likely always use a combination of CAN and Ethernet, the eventual transition to an automotive ethernet backbone is inevitable and for good reason. The new generation of vehicle software supporting the driver-centric experience requires support for increased communication needs.
Switching to Ethernet also comes with some downsides including a more costly controller and physical-layer interface, complicated EMC issues, and overheads relating to real time communication such as TSN. The advantages, however, significantly outweigh the disadvantages, making this transition a crucial next step in the continued growth of the automotive industry.
The transition to automotive Ethernet will provide the following benefits:
- Significantly higher throughput rates (up to 10 Gbps) will be supported with multiple CAN buses aggregated to a single Ethernet link. This means less wiring and lower installation and maintenance costs.
- Quality of service (QoS) and time-sensitive networking (TSN) will be supported, allowing for real-time communication and the transmission of lower priority data at the same time.
- Advanced security features will protect highly-connected vehicles from hackers and viruses.
- As new components are upgraded or added, they can easily be connected (and old ones disconnected) using Ethernet’s plug and play capabilities.
All that being said, given the investment already made in CAN systems, the costs of a complete and immediate switch to Automotive Ethernet are not currently a viable option. As automotive architectures continue to evolve, Automotive Ethernet will be adopted more often alongside the legacy architecture until both technologies will be utilized optimally as CAN and LIN are today.