Entering the Ethernet Era: The Difference Between CAN and Ethernet
June 20, 2023
Yuri Friedman
Product Manager
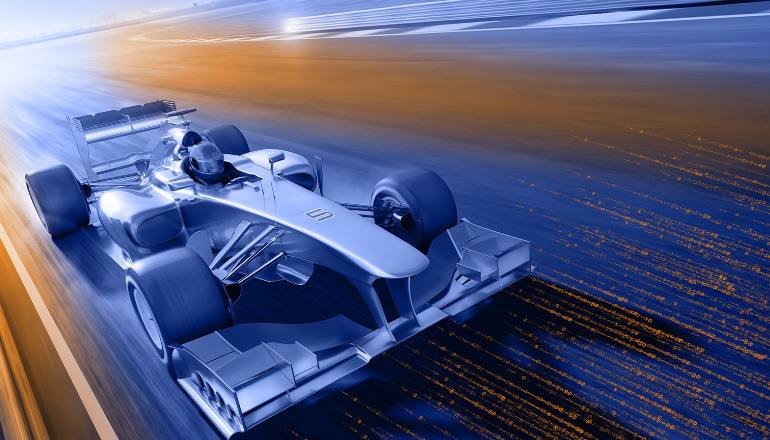
The software-defined vehicle is designed to optimize the driver’s experience. Its advanced software capabilities require a high-performance hardware foundation, and the legacy CAN bus networking backbone is stretched to its limit.
The biggest problem with CAN is its limited bandwidth. At best, it can provide 5 Mbps payload throughput (i.e., goodput) with the newer CAN-FD, which is pretty meager by today’s standards. However, because CAN is reliable and cheap, automakers have resisted changing it and they have been adding CAN buses to provide additional bandwidth. But this is far from ideal.
SDVs require stronger underlying tech capabilities to support new functionality, and Ethernet, proven in avionics and industrial applications, is perfectly suited to high line rates, higher payloads and higher resulting goodput.
Let’s take a look at the difference between CAN and Automotive Ethernet and see what the future holds for the automotive industry.
CAN is at the Heart of the Vehicle…
The CAN revolution in automotive technology took place in 1991 when CAN buses were first deployed. The CAN bus quickly became the norm, acting as the heart of the car’s networking system. CAN’s popularity took off, as some of its key technical features made it the perfect match for cars’ needs as it:
- Replaces multiple discrete I/O lines with one 2-wire message bus
- Runs in realtime
- Has a physical layer and protocol resulting in high tolerance for noise
- Supports native multicast and broadcast
- Offers built-in frame priorities
- Supports non-destructive collision resolution
- Has 100% distributed in operation
- Supports long single buses
- Is low-cost to build
Despite all of its upside, the CAN bus has significant limitations as communication demands continue to grow. The number of devices for each CAN bus is constantly increasing and with its low data-transmission rate of 5 Mb/s (CAN-FD) or 1 Mb/s (CAN), each new device significantly decreases its performance.
As a first step towards addressing the new demands for software-defined vehicles, car manufacturers have continuously added additional CAN buses to the car’s infrastructure. While this has worked until now, it isn’t a scalable or cost-effective approach as it requires adding significant amounts of wiring and complex gateways. It also leaves connected cars more vulnerable to cybersecurity attacks.
...But Ethernet Provides a Stronger Backbone
Compared to CAN, Ethernet offers a strong solution to the problems raised by the traditional CAN bus architecture. SDVs need a high-performance backbone that can support the increased communication from the new software creating the driver-centric experience. Trends are showing carmakers moving away from more traditional complex wiring to a Zonal Architecture that relies on Ethernet to run smoothly and securely.
The advantages of Ethernet to CAN include:
- Supports significantly higher throughput rates (up to 10Gbps and working on more), allowing to aggregate multiple CAN buses into a single Ethernet link. This results in smaller wiring harnesses than CAN, meaning lower installation and maintenance costs.
- Supports quality of service and time-sensitive networking (TSN) for allowing real time communication to be multiplexed with lower priority data.
- Advanced security features and transport layer services
- Plug and play capabilities mean components can be connected and disconnected as needed with automatic detection and configuration
The downside to Ethernet is that it includes a more costly controller and physical-layer interface, complicated electromagnetic compatibility issues, as well as overhead for allowing for realtime communication (e.g. TSN). But the bad doesn’t outweigh the good in the question of automotive Ethernet vs. CAN.
Overall, the inherent flexibility in Ethernet is what gives the edge to architectures that use it for their communication backbone. Especially as more and more lines of code are added to car models, the choice will sway even more to Ethernet as that will better support the multitude of infotainment, safety, and autonomous driving features along with over-the-air updates.
So Who Wins? Ethernet or CAN?
While all indications point to Ethernet taking over with predictions of the Ethernet market growing from $10.74 billion in 2021 to $18.59 billion by 2030, we haven’t seen the last of CAN buses either. We are already seeing in some models a combination of CAN and Ethernet complementing each other.
As automakers move to Zonal E/E Architecture, there will still be instances of newer ECUs that need to operate alongside legacy ECUs that do not yet need to be replaced. In such cases, it is more cost effective to continue using CAN for the legacy parts and adding Ethernet for newer components. One attempt to replace CAN altogether comes in the form of 10Base-T1S Ethernet, which reduces Ethernet’s costs significantly.
While there are some technical issues (EMI/EMC, costs, complexity, wire length limitations, etc.) that need to be addressed before Ethernet becomes a widespread replacement to CAN and CAN-FD, there are solutions on the market that offer legacy system support along with the benefits only available from Ethernet. The GuardKnox CommEngine™ is a high-performance and cost-effective communication routing solution. It provides efficient gateway functionality and supports all common, and custom, automotive interfaces to enable automotive manufacturers and Tier 1s to leverage both legacy and new networking technologies in a seamless and cost-effective way. Click here to get in touch to learn more.